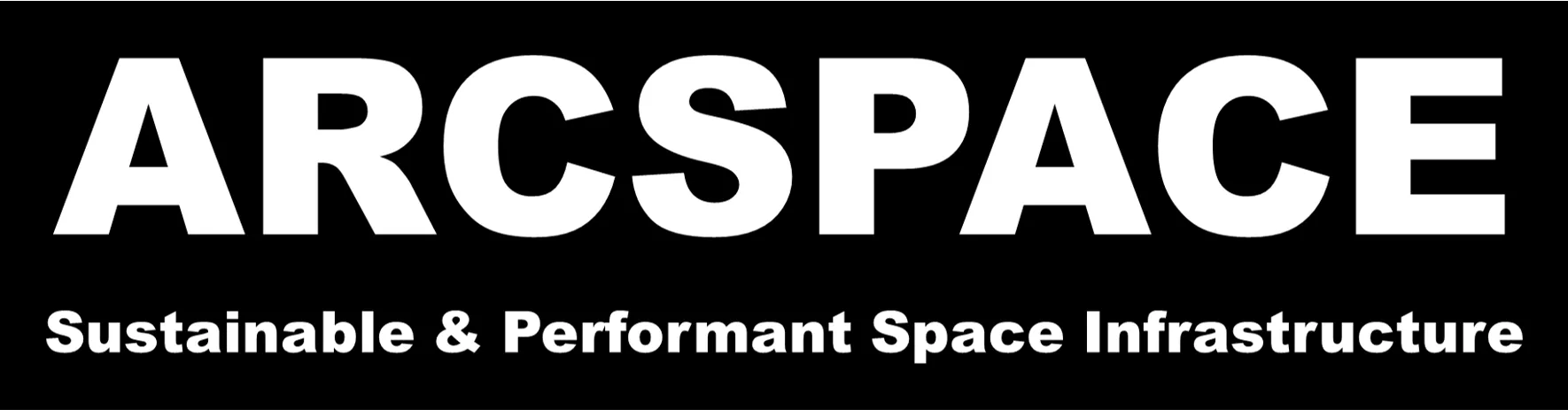
ArcSpace
About your organization / profile
Problem-Statement & Innovation
In-Space Servicing, Assembly, Manufacturing (ISAM) is the next frontier for the growth of the space economy: it disrupts the way we design, build and operate everything we send into space. And yet, over 20 years of developments has only led to a handful of demo missions. This is due to the complexity (cost, time, risk) of developing such missions end-to-end, as made apparent with NASA’s OSAM-1 mission recently canceled or ESA’s ClearSpace-1 mission challenges.
Validating and qualifying subsystems in situ is critical due to the fact that Space is a unique environment (microgravity, vacuum, radiation…) which cannot be accurately reproduced on Earth. Current alternatives involve computer simulations based on physical modeling and partially reproducing vacuum, thermal, reduced gravity conditions for a limited amount of time with test campaigns costing hundreds of thousands of euros. The data obtained is often incomplete, difficult to correlate to real operating conditions and require significant time for analysis.
For these reasons, developing on-orbit testing, validation and qualification capabilities dedicated to ISAM and ISRU needs are critical for companies to offer competitive commercial solutions in the market.
Our solution
ArcSpace provides an orbital testbed platform for technology validation and qualification, dedicated to ISAM and ISRU needs. Located in LEO, the platform hosts two robotic arms, robust attitude and robotics control algorithms, 2kW power and proprietary equipment including materials processing and precision tools for robotic assembly.
The platform enables open-space robotic manipulation with real-world thermal, vacuum, radiation, illumination, microgravity and structural response conditions which provide a complete and accurate validation of in-space operations. This allows customers to qualify a diverse range of in-space servicing use-cases, ranging from close-range/proximity operations to in-space assembly hardware and software algorithms performance. Customer robotic control and attitude control algorithms can be uploaded and validated under orbital conditions for their specific use cases and demonstration requirements.
The onboard capabilities include a proprietary electron beam unit for microgravity processing: 1) space welding, 2) cutting, 3) drilling, 4) vaporization and 5) deposition processes in a safe and non-debris/contamination generating environment. In addition, the platform is equipped with high-accuracy self-aligning robotic tooling equipment that enables a wide range of in-space assembly demonstrations. The high onboard power made available through standardized HOTDOCK port allows testing of energy-intensive payloads such as microgravity 3D printers and power tools for ISRU.
Through ArcSpace’s solution, space companies, institutions and research institutes are able to fast-track their developments of a wide range of manufacturing and operational technologies in space and reduce risks in a cost-effective and agile manner.
Business Model
ArcSpace’s business model is a platform-as-a-service. We provide customers access to the Orbital Testbed Operations Platform (OTOP) for hardware, software and science activities. We ensure that client operations comply with platform specifications, integrate and operate the onboard tools and provide output data and insights to the end-user.
Unique Selling Points
The platform services offered by ArcSpace are dedicated to ISAM and ISRU needs. We enable open-space robotic manipulation and control algorithms testing for customers to validate and qualify their operations in the exact environment of their commercial applications: this provides faster and more accurate data for qualification of their services which other platforms (orbital and ground-based) cannot compete with. The attitude control, available power and instrumentation (sensors, data analysis) are the onboard selling points, as they unlock advanced on-orbit robotic manipulation for multiple applications that are not available elsewhere for testing and validation.
The proprietary tools made available to customers on the platform enable material processing in microgravity, including a patented space welding unit for joining, cutting, drilling in microgravity via a safe and no-debris/contamination generating process. The hours to months-long operations allowed by the platform are disruptive compared to alternative <30s microgravity generated by parabolic flight tests and sounding rockets. A second tool provided is a precision tool end-effector that allows sub-millimeter accuracy assembly operations.
ArcSpace’s innovation lies in its two core technologies, namely the space welding unit and dedicated control software for complex microgravity robotic operations. Together, they provide the aforementioned unique selling points but also provide requirements for the platform that fit commercial needs, which other competing platforms do not address.
Network (0)
There are no organizations in the network.
Recent activities
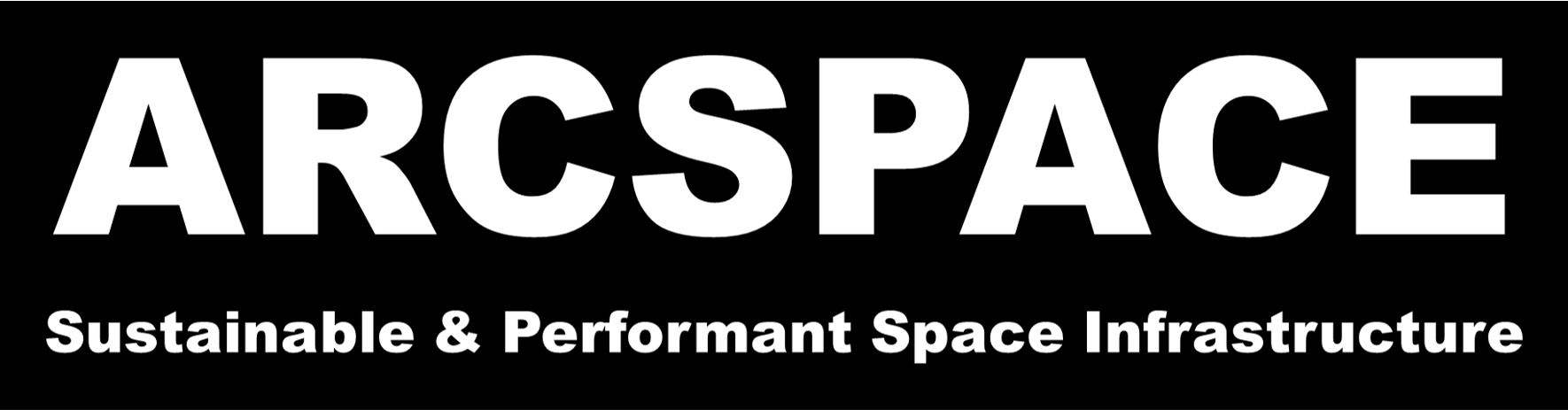
ArcSpace is now a member of the EIC Accelerator France community.
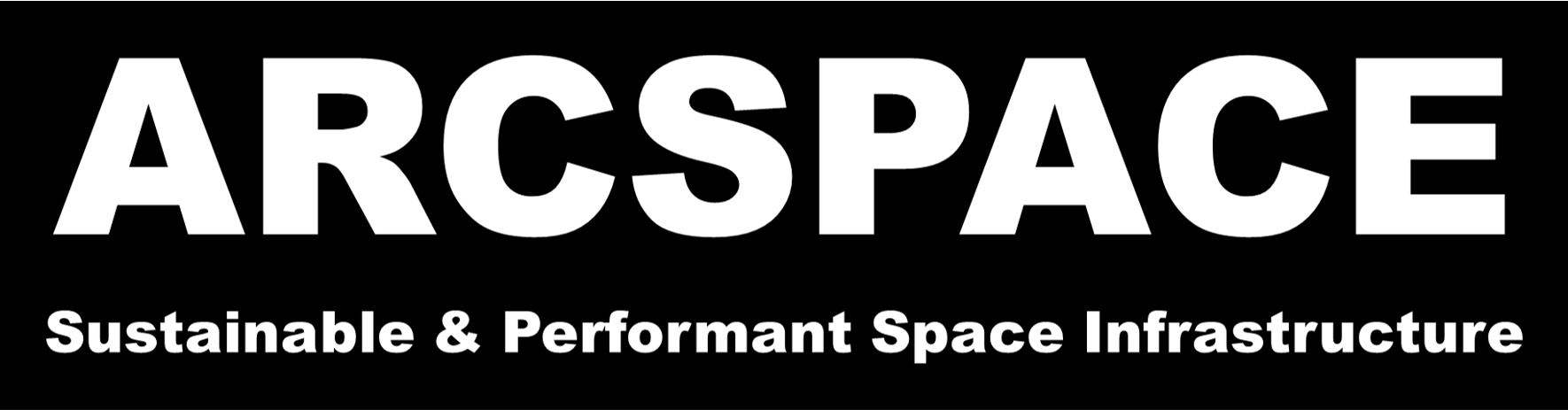
ArcSpace has taken its fundraising offline.
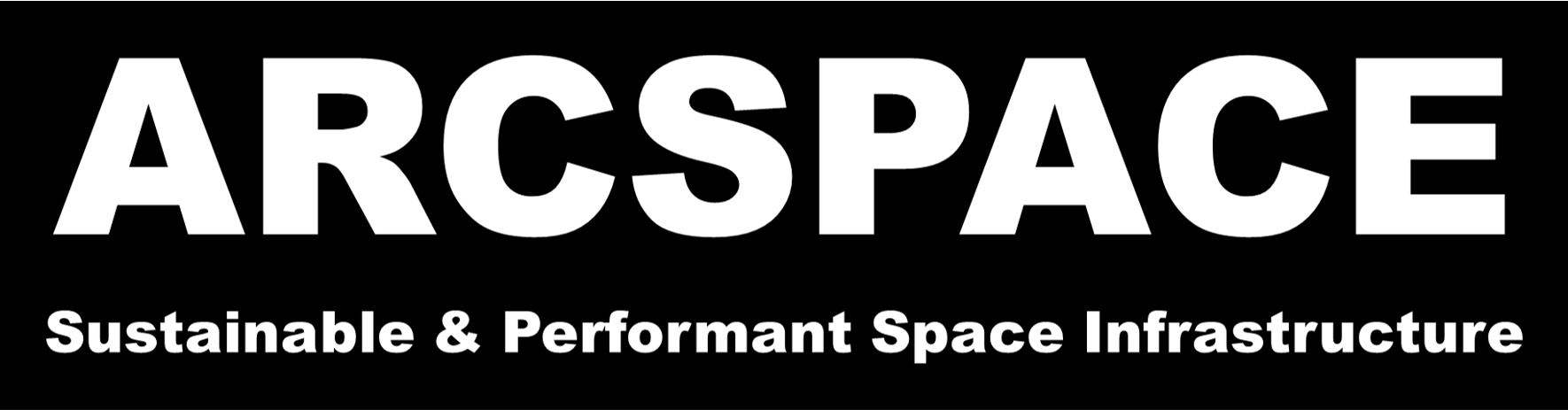
ArcSpace is now a member of the Enterprise Europe Network FRANCE community.
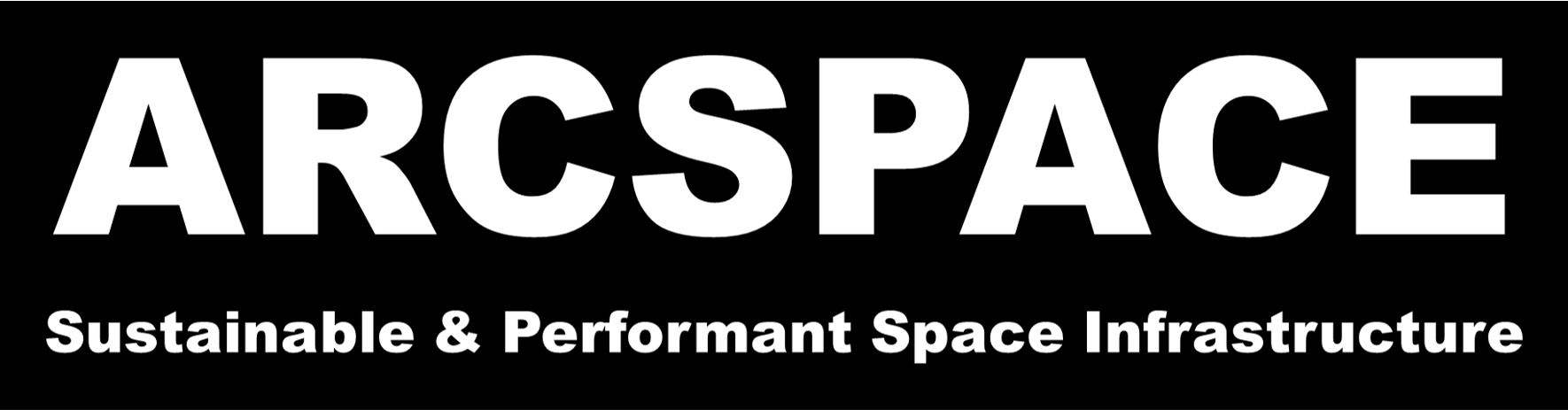
The pitchdeck document has been updated in the dataroom.
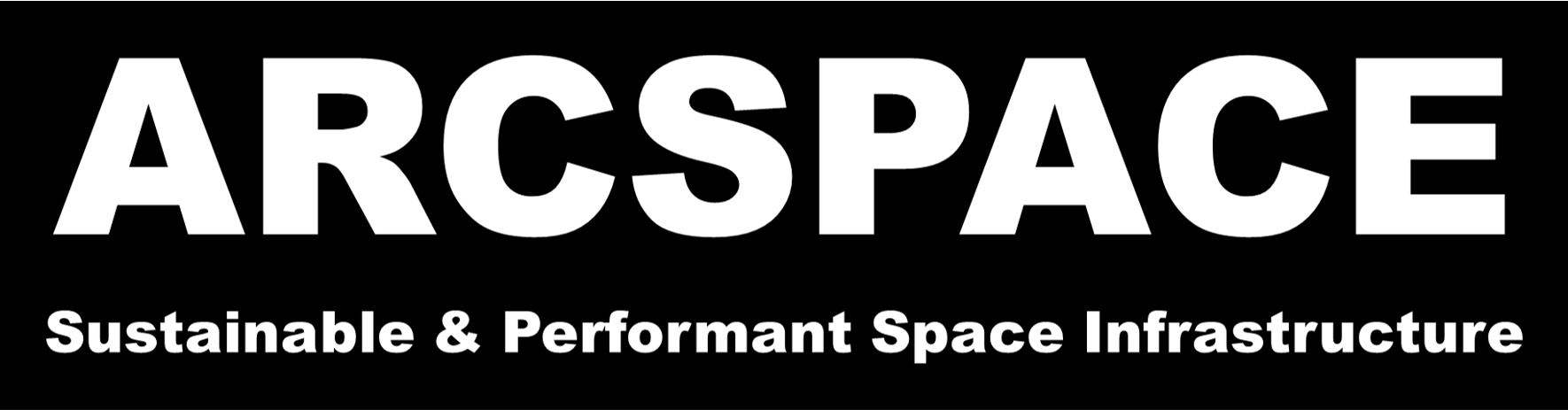
ArcSpace has updated its fundraising.
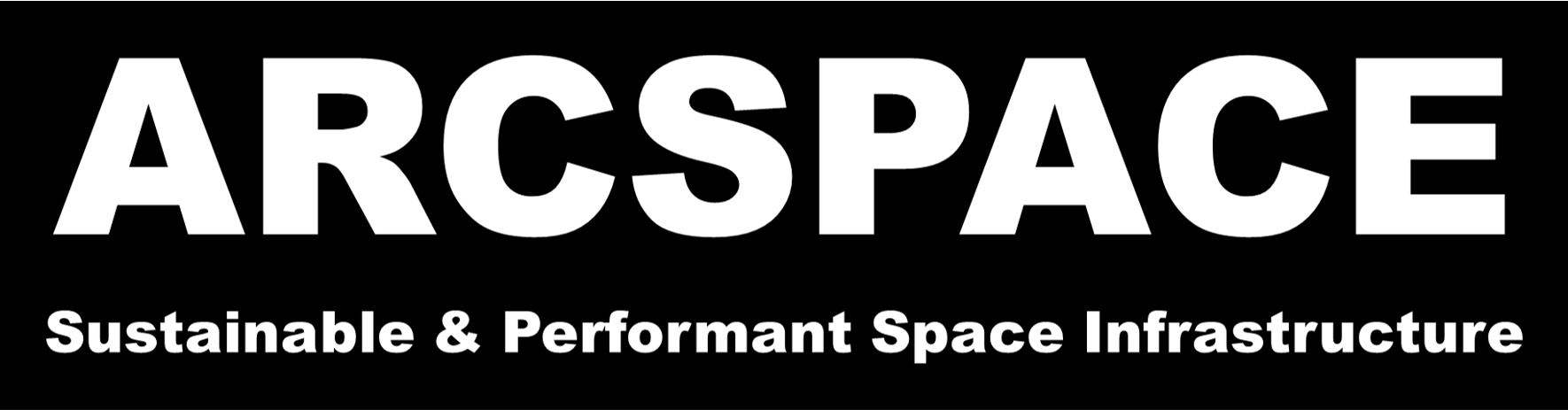
The pitchdeck document has been updated in the dataroom.
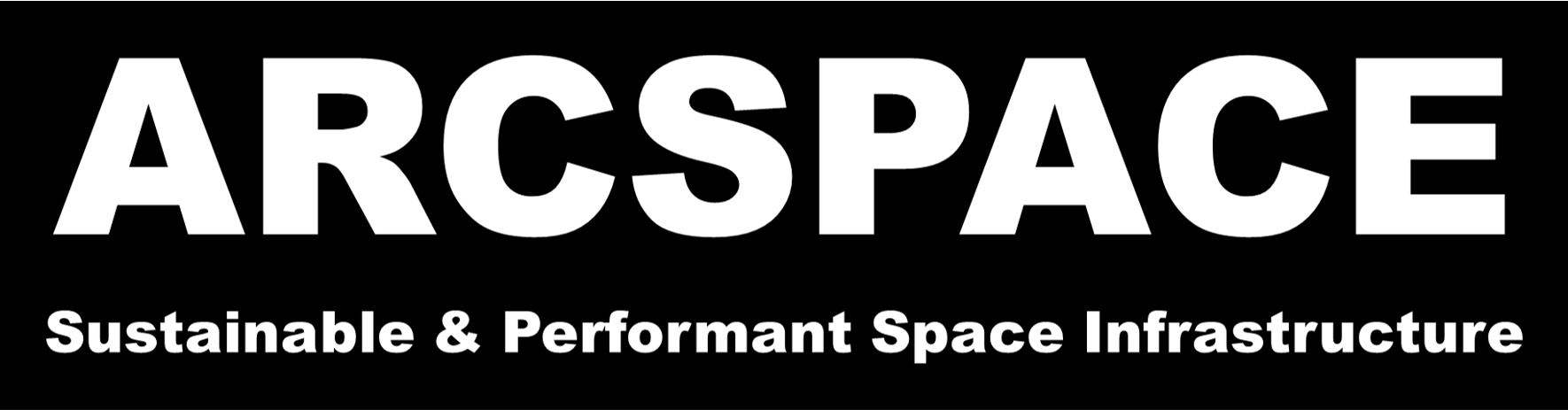
ArcSpace has published fundraising documents.
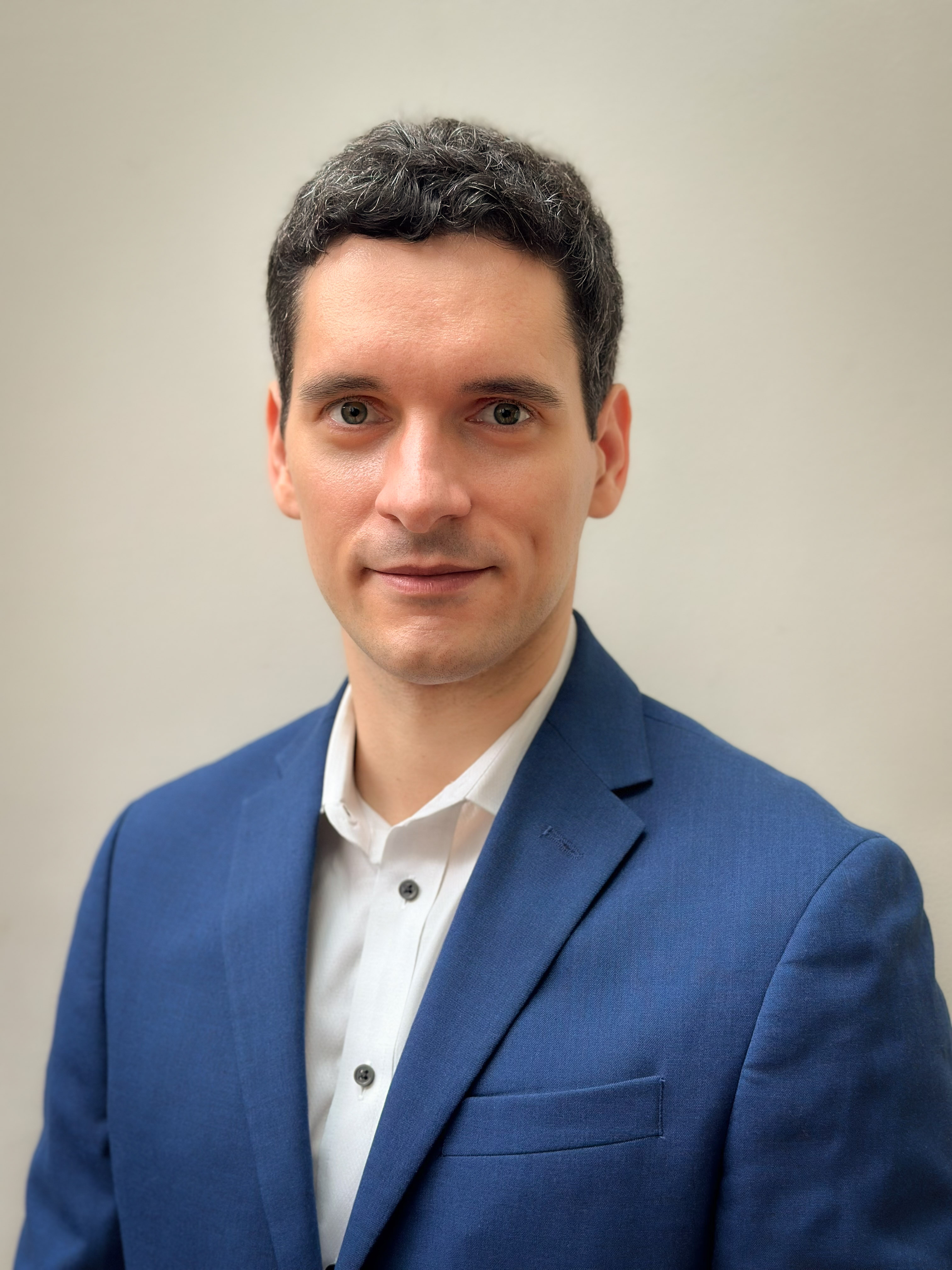
Guillaume Mohara has joined ArcSpace.